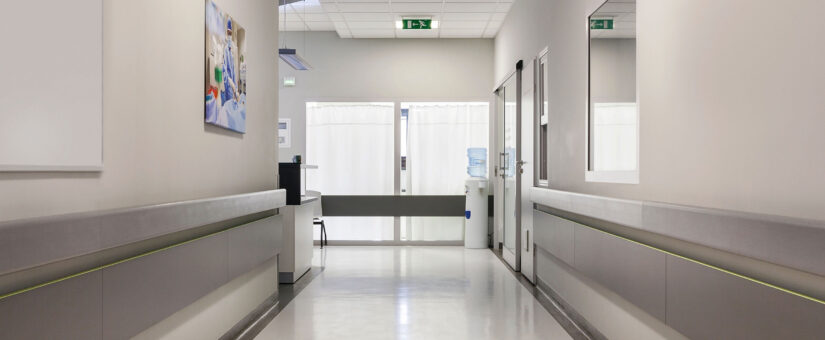
Making a Coved Floor
Coved floors are great where water and fluids are regularly expected to be part of the environment, or where sanitation regimens are regular and crucial. They are also beneficial when rooms and hallways see a lot of traffic with hand carts, trolleys, and other equipment that often bumps into the walls. With coved flooring the walls are protected for anywhere from two to about eight inches or more by raising the epoxy flooring up from the floor and onto the lower surface of the walls. This brings the protective benefits of the epoxy coating onto the wall itself. California Custom Coatings has a lot of experience with installing coved floors in Sacramento, Northern California, and beyond.
How We Install Coved Floors
There are seven stages to installing a coved floor. As you will note, it takes considerable experience and even some art to do a coved floor correctly. It is definitely not a do-it-yourself process, as the epoxy needs to be molded swiftly, yet carefully.
Step 1: Prepare the Surface
The surface cannot have any dirt, paint, wallpaper, or grime on it. A porous surface is required for the epoxy to attach properly. Prepping the surface with care is essential.
Step 2: Strike the Line
Depending on the customer specifications, we mark the top of the cove along the surface of the wall. Then we mask that line to protect the wall surface that will not be coved. This is critical to create a level, even top line for the coving.
Step 3: Add Primer
A primer coat must be laid on the wall to ensure that the epoxy adheres properly. Just the right amount is required, because too much primer creates unwanted runs that affect the finish. Depending on the surface material, a second coat of primer may be required.
Step 4: Mix the Epoxy
All epoxy coatings have a limited amount of application time. For installing coves, respecting this time is very important. Add to this fact the additional problem that the primer is effective only between the window when it is tacky, but not yet dry. Professional experience gives the staff at California Custom Coatings the ability to recognize when the primer is ready, to mix up the epoxy coating efficiently, and to get it applied before it dries out and wastes material.
Step 5: Make the Cove
Using a trowel, we apply the epoxy to the wall and near the floor space. The result creates a smooth bevel from floor to wall at the bottom and a smooth ridge at the top. When the application is complete, we remove the masking tape, leaving behind a sharp ridge at the top.
Step 6: Seal the Cove
Just like the floor, a cove needs to be sealed with a protective top coat. We also add any additional elements, like flakes or metallic micas, to the cove during this process. The effect is meant to be seamless, both in fact and in appearance.
Step 7: Install the Floor
Once the cove is complete, the rest of the floor is installed to match. The end result is a seamless barrier from wall to wall, protecting the floor and the lower walls from liquid and scuff damage. Full customization of floor and coving is possible with help from California Custom Coatings.
For more information about coved flooring for your property, contact California Custom Coatings online or by phone.
- On July 11, 2024